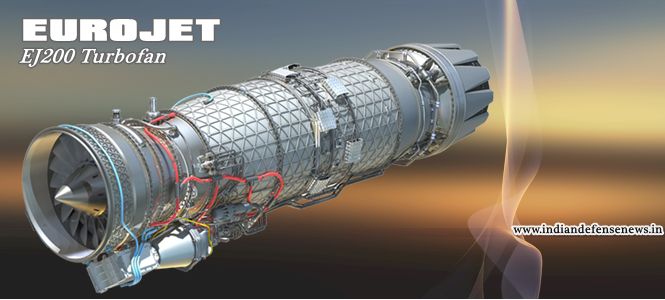
Amongst futuristic defence development programs in India is the Advanced Medium Combat Aircraft (AMCA) presently at the designing phase at the Aeronautical Development Agency (ADA) at Bangalore. The AMCA endeavours to proivide the IAF with a superlative combat aircraft capability of the next generation.
Perhaps the most critical element for the AMCA is the power plant and the IAF is well aware of the need to identify an appropriate engine that will not only power the AMCA but have the potential to "grow" in the years to come. Among the shortlisted or should I say the desired engines by the lead integrator ADA is the Eurojet EJ200 Turbofan which powers the Eurofighter Typhoon, one of the world's most advanced 4+ fighters, and just as in the Typhoon for which it was built, the EJ200 on the other hand would fit the bill for the AMCA with consummate ease.
Unlike the Indian Navy, IAF is lagging behind in the indigenisation process by a distance for its planned airborne requirements. The Indian Navy has by far the most robust and focused localization program amongst the three armed forces. To bridge this yawning gap and to address the issue the IAF is keen to rapidly adopt modern technologies.
During the 10th edition of Aero India 2015 this author spoke to executives of Eurojet with regard to the opportunities of building the EJ200 in India, they expressed strong willingness to build a long-lasting relationship with not only the IAF but also with India's aeronautical industry whose world-class partnership practices could bring several advantages to the industry by creating and sustaining turbofan technology solutions which India is currently lacking.
One of the challenges facing the government is the need for investments in increased technology across the defence forces and the necessity of balancing the budget over simultaneous requirements. In order to make this available the IAF must seek mature and appropriate product mix which adds full capability for growth.
In this context, Eurojet offers a level of technology that is second to none and offers a system that has outperformed the specifications right from day one. ADA can adapt the EJ200 for the project which is readily available today while achieving a solution that fully supports the unique requirements for the AMCA.
Features the EJ200
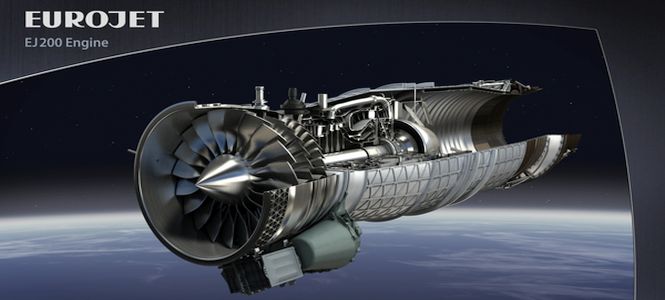
The EJ200 is a twin shaft reheated military turbofan, with three low pressure (LP) and five high pressure (HP) compressor stages, powered by two single-stage turbines (LP and HP). The engine is largely based on the Rolls-Royce XG-40 technology demonstrator which was developed in the 1980s.
The Eurojet EJ200 features many state of the art design elements, including integrated blade/disk construction, (blisks) wide chord fan airfoils without a need for inlet guide vanes, single crystal turbine blades, an airspray fuel delivery system, and an advanced FADEC system for engine control and onboard diagnostic systems. The engine is classified as a low bypass ratio augmented turbofan engine, because its low pressure compressor feeds some of the airflow to a bypass duct, and the augmentation refers to its afterburning capability. A low bypass engine such as this is very well suited to a modern fighter; it is a perfect compromise between a turbofan engine, which provides high engine efficiency, low heat signature, and great engine response and low speed performance, and a turbojet, which provides low engine profile and compact size, and great high speed peformance and efficiency.
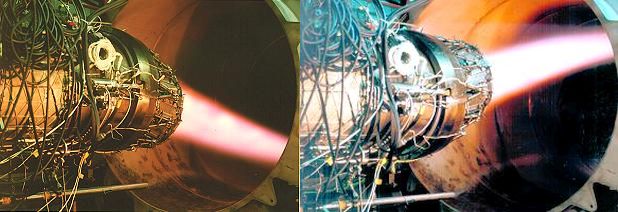
Rig trials of EJ200 Turbofan Engine
The engine is fed by a variable geometry inlet duct on the Eurofighter, making it difficult for enemy radar to home in on its spinning fan blades, while tailoring the airflow for varying inlet conditions. The air is drawn into the compressor inlet, which features no inlet guide vanes. The three stage wide chord low pressure compressor is classified as a fan, because apart from feeding the high pressure compressor in the engine core, it also feeds the bypass duct, which bypasses air around the engine core, surrounding it in a cooling blanket, which allows for higher combustion temperatures and turbine inlet temperatures. The engine features a bypass ratio of .4:1. The high pressure compressor has five axial stages and brings the pressure ratio to a staggering 26:1. Compressor discharge air is fed to an annular through-flow burner which utilizes air spray injectors to distribute fuel into the burner.
Discharge air is injected into the fuel vaporizing nozzles which aids in the atomization of the fuel, allowing for more complete fuel distribution and more complete combustion, which of course leads to better fuel efficiency. Maximum turbine inlet temperature is a metal-melting 2,700 degrees fahrenheit, so the high pressure turbine nozzle and the turbine stages must be air cooled with bleed air, and they must be single crystal formed of exotic metal alloy compositions, with a ceramic thermal barrier coating to further protect the blades from meldown. The high turbine inlet temperature leads to tremendous efficiency and specific power. There are only two turbine stages on this engine. A single stage axial high pressure turbine drives the high pressure compressor and the accessory gearbox, and the single stage axial low pressure compressor drives the fan. After the gas has been expanded through the turbines, the remaining gas energy is available to provide thrust. The hot gas is expelled into the afterburner or augmeter, which is a tapered jet pipe with a fuel manifold and combustor integrated. It is here that the hot combustion gas is mixed with the cool air from the bypass duct.
The availability of uncombined oxygen from the bypass duct makes the afterburner even more effective than in a pure turbojet. When the pilot moves the power lever into the afterburning region, fuel is distributed to the afterburner fuel manifold, and the afterburner igniter is triggered, providing a marked increase in thrust along with fuel consumption. The pilot can vary the amount of afterburner by modulating the power lever within the afterburning range. The end of the jet pipe forms a throat which accelerates the gas flow before it enters the variable geometry divergent jet nozzle. The convergent/divergent nozzle system effectively accelerates the gas flow to supersonic speed, and then allows it to expand smoothly with the outside airflow for maximum efficiency and thrust.
The variable geometry nozzle varies nozzle area to optimize gas flow for a given engine regime. At low power, the nozzle is wide open, to minimize residual thrust and improve low speed engine response. As power increases, the nozzle area closes down to accelerate the gases at a higher velocity. When the afterburner is in use, the nozzle once again opens to accomodate the greater mass flow out of the tailpipe. The accessories are driven off the high pressure shaft. Accesories include oil pressure and scavenge pumps, high and low pressure fuel pumps, a DC generator, a hydraulic pump, an air turbine starter, and spare drives. Engine control is by an advanced FADEC system, which provides precise power control, ultra rapid response, and diagnostic services.
The Engine's average time on wings is 1,120 engine flying hours with the lead engine achieving an excess of 1,700 engine flying hours on wing which demonstrates its unbeatable and proven reliability. The unique modular construction of the engine allows for quick repairs by modular exchange, with low engine turn around time, the design achieves considerable Life Cycle Cost savings and involves very high levels of automated assembly integration during the maintenance process.
The EJ200 is a lightweight, efficient and powerful state of the art military engine which emphasizes the advantages of a simple design combined with cutting edge materials and electronic technology which could suit the expectations of one of India's most prestigious and crucial defence projects because the Eurojet EJ200 offers unrivaled technology and reliability. (Adapted)